There are many factors you should consider to make an informed decision about the level of automation for your cartoning machine.
Are you considering automating your cartoning processes? If you are not sure how to choose the automation level for your cartoning machine that is best suited for your company, our blog post can help you understand different automation levels. We have previously written about indicators that show when packaging automation is the logical next step. But, when your printing volume of folding cartons reaches high levels, it is not just about deciding to include automated cartoning equipment. This is a very complex decision, as there are different levels of automation and various equipment available on the market. Making the right choice is crucial to ensure that your company will feel all the benefits of automation.
As every business is unique, there are no universal solutions that apply to everyone. Management needs to consider many factors during the decision-making process. To justify the investment cost, equipment needs to be specifically tailored to your company's packaging processes. The research needs to be extensive, and the choice of your partners well thought out. Having a reliable partner is crucial for successful automation. The equipment supplier should be interested in your business, and ready to answer all your questions. They should offer advice, assistance, and training for your employees. The equipment should be adjusted to fit your needs.
Steps To Take When Choosing Cartoner
Some steps can help you determine the level of cartoning automation your company needs based on your retail packaging printing needs and the packing processes:
Mapping Your Processes
There are new different processes in every stage of company growth, on every level. It is vital to map them correctly. Knowing what, when, and how it is currently done in the packaging process is necessary to make changes and create more effective and efficient processes. This will also help the management and your automation partners successfully determine what equipment is the best choice for the company. After you map the current state of your packaging process, you can determine the bottlenecks and think of ways to improve your process. Although your equipment supplier should be heavily involved in this, nobody knows your business as you do. You have to make sure they are not missing any part of the packing process when they are adapting the machines.
Consider the Product
The type of the product will dictate the equipment your company can use. For some products it is a good idea to use vertical equipment, if they are free flowing. However, for most products horizontal cartoning equipment offers more flexibility at a lower cost. Also, consider your production plans for the future, and, if possible, choose a flexible cartoning solution that will make future adjustments easier.

Consult Your Packaging Supplier
Nobody knows your business better than you. But, acknowledge the fact that your suppliers know theirs. They can help you determine the best course of action. The printer has employees who can advise on the type of paperboard packaging that will best suit both your products and the equipment you plan to buy. It wouldn't be good to invest in the equipment and then find out later that it does not work for your retail packaging. And your product can't be packed in the type of packaging that the equipment can work with. This risk can be avoided if you involve your packaging supplier in the process from the beginning. Let them help you decide on the best packaging option before investing. The type of paperboard will affect the effectiveness of the equipment. Make sure you test the equipment with the exact materials you will use, before making the final decision. If you trust your retail packaging supplier to take care of your printing needs, you should also trust them to advise you.
Include Your Employees
They are the ones on the floor, doing the work. Nobody can tell you just how the processes look or what the bottlenecks are better than them. They have firsthand experience with the packing process. The information you can get from them is invaluable. Don't let the management get caught up in how they think the process looks. Employees who interact with printed packaging and the product are the ones who can also help you determine the best course of action. Make sure you get all the information you can before making such an important decision.
Different Levels of Cartoning Automation
Manual Cartoning
This is the starting point for most businesses. The entire process is done manually. This makes sense for products still finding their place on the market, when the demand is low. Your packing process is entirely dependent on your employees. As the demand grows, most businesses are automating their cartoning processes to at least some extent.
There are solutions for transition periods that can help you quickly improve your cartoning processes while preparing for automatization. Note that these transitional solutions' productivity improvements are limited to 10-25%.
One of these solutions is using collecting tables and conveyors. They serve as a help to the manual processes. But don't confuse them with automated machines. There is no automation included with this equipment. It requires manual work, and your packing process will remain dependent on manual labor, with all the costs and risks associated with this. The productivity levels will vary depending on your staff's energy levels, and human factors will cause mistakes. They are fixed, and you can't modify them to suit your company better.

On the other hand, they do improve productivity and are the least expensive solution to achieve this goal. They are also easy to implement and do not require extensive training.
When you have small production runs with many variations and changes, collecting tables and conveyors are an excellent first step you can take. They can make manually putting the product in the paperboard packaging easier.
Further improvement is possible by adding additional peripheral devices, making them semi-automated.
Semi-Automated Cartoning Machine
Semi-automated process means at least one automated function. This optimizes productivity and efficiency to keep up with growing demand. Having at least one automated feature improves the speed of the process, but a man still operates the machine.
Semi-automation is the perfect choice if you have complex retail boxes or a wide range of boxes. Also, it is a good choice for companies with diverse product mix. This automation level is suitable for companies with variable production runs (2000-4000 per day) that use small or medium-sized paperboard boxes.

As these machines are still very human-dependent, using them allows for your staff to ensure every switch is done correctly. It is more efficient than the manual packing process but allows for quick adjustments. It is a favored choice for companies that use diverse box formats or complex boxes that require constant quality control checks and adjustments.
Semi-automated cartoning machines have easy installation, setup, flexibility, and added quality control.
The negative side is that it is not top speed and needs human supervision to function correctly.

Automated Cartoning Machine
The process is considered automated when a machine is the critical factor of your cartoning process. Although the operators still need to be there, they only need to perform background tasks. This allows them to avoid physically straining tasks, which improves team member satisfaction. Automatic carton filling machine is a solution for companies with longer production runs and a limited variety of printed box formats that do not require constant adjustments.
Automated cartoning equipment is not limited by human factors regarding productivity. Depending on how well the processes were mapped before automation, you can raise your productivity by 50-100%. Human errors are avoided with this equipment. Also, there is less need for your staff to do labor-intensive tasks. The machine does repetitive tasks, which frees your employees' time for creative and more challenging work. Also, machines can handle large boxes much more efficiently than humans can.

On the negative side, automated equipment costs more than semi-automated. Also, these machines are less versatile, as they are made for focused tasks. They are harder to move, and setup time is generally longer than with semi-automated equipment.
This is just the reason the decision to invest in automated cartoning equipment shouldn't be taken lightly. But, if the decision on which automatic cartoning machine to invest in is well thought out, it should be tailored to the needs of your processes before the installation. And it should bring in so many benefits to the company that it highly exceeds the expense and any potentially negative aspect of automation.

Fully Automated Cartoning Equipment
Fully automated processes are automatically managed. Humans still have to perform setups and adjustments, but they do not require the presence of operators while running. These robotic lines help reduce labor intensity and production personnel. This makes them perfect when it is hard to find an unskilled labor force.
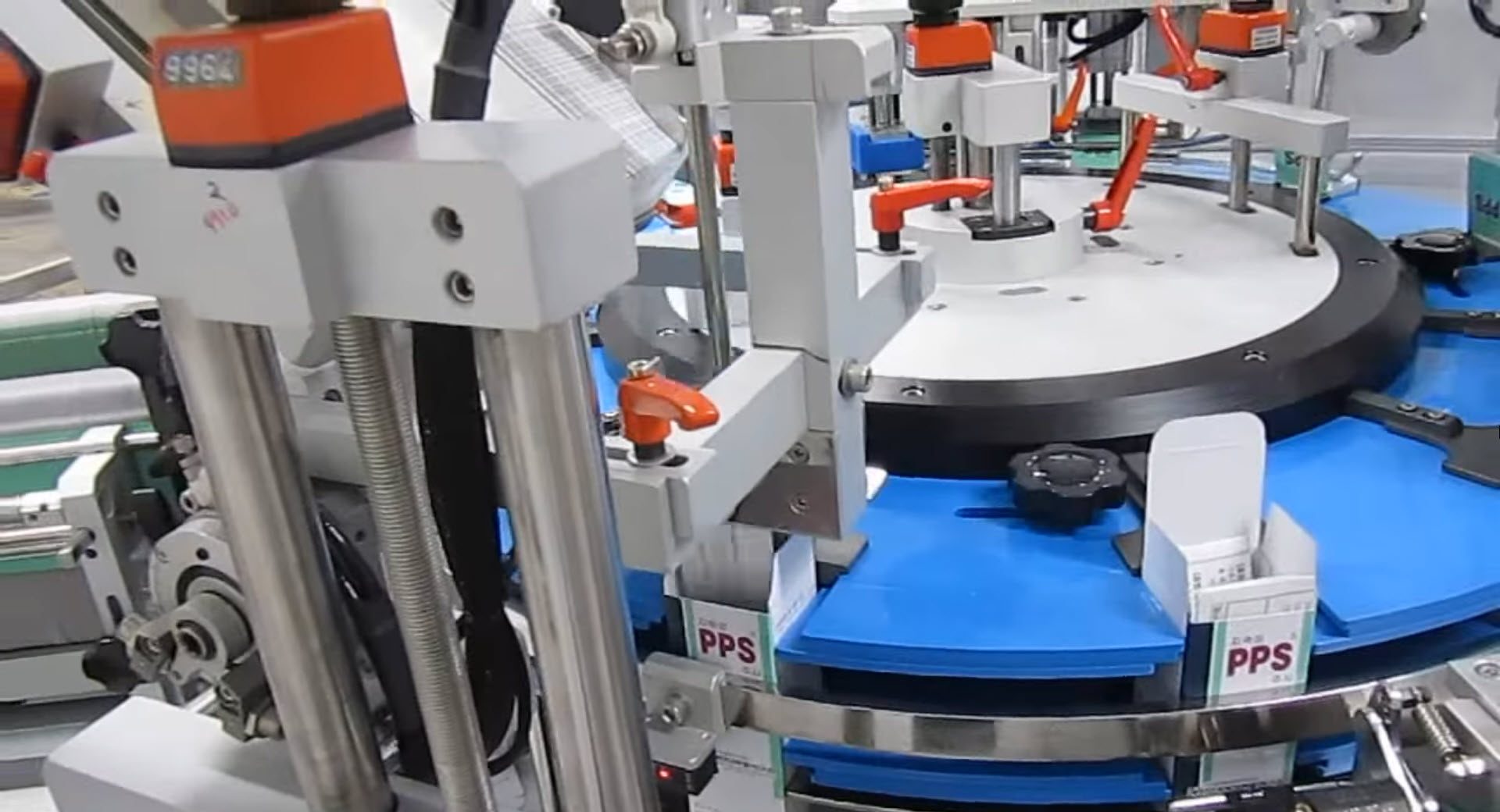
It is a perfect fit for companies that need extreme productivity. If your production reaches above 10000 units per day or shift, it is an excellent time to consider full automation. Fully automated equipment offers high production speed to companies with constant production. These machines are more costly and complex than any other option. Also, they require strict safety measures and skilled operators for maintenance. However, a fully automated cartoning machine reduces safety hazards during production and entirely eliminates the risk of human error once the setup is correctly done. This means that there is almost no risk of damaging the product or the packaging.

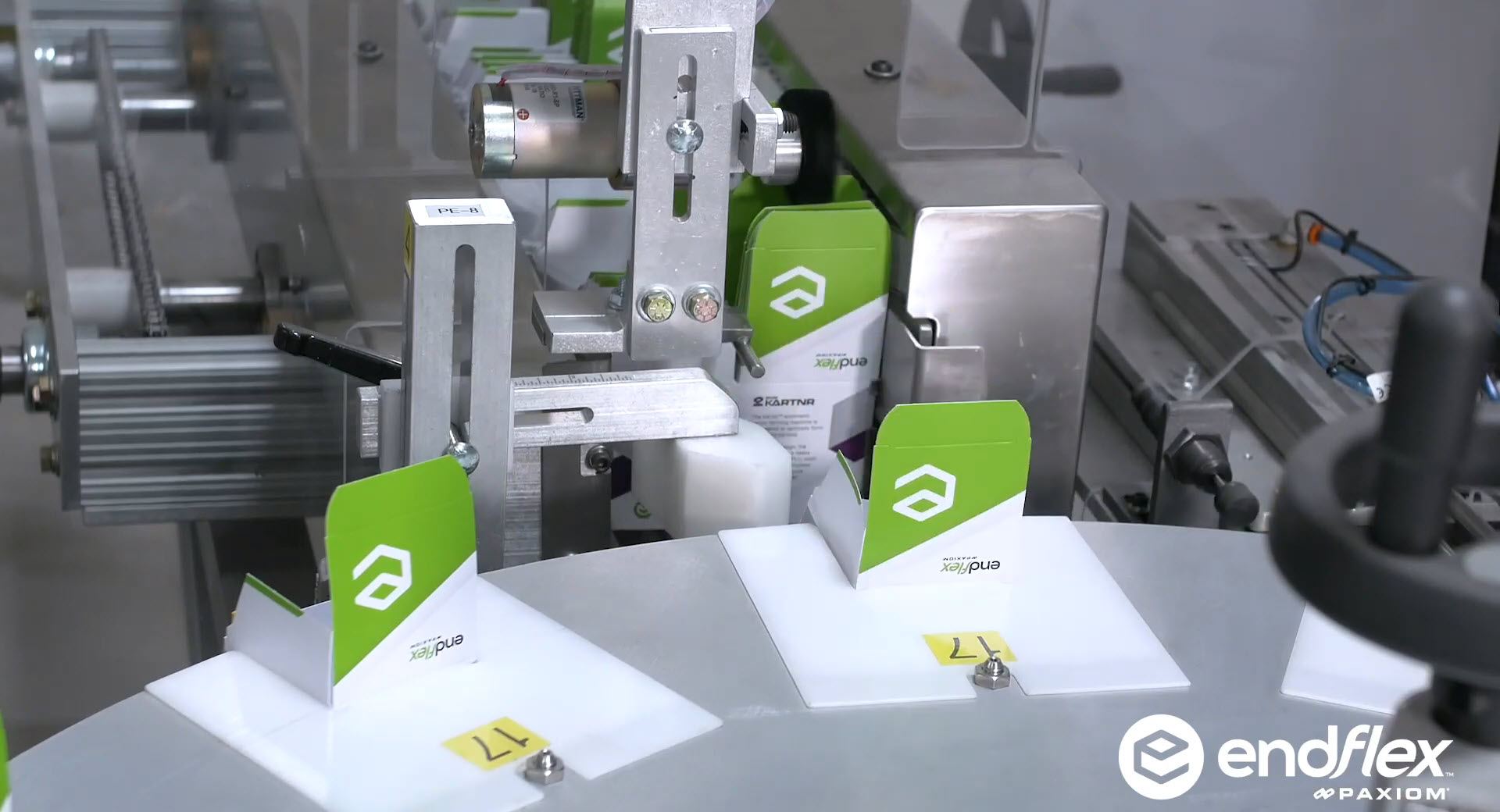

If you are still unconvinced that automation is the future, you can read about the cartoning machines market in Fortune Business Insights.